As a full-service CDMO, we’re able to offer a suite of services: from device development and human factors engineering, to rapid prototyping, mold tooling, injection molding, and cleanroom assembly.
Our end-to-end capabilities allow us to accelerate time-to-market while ensuring the highest standards of quality for our medical and pharmaceutical customers.
In this blog, we explore the process of bringing injection molded components to life for use in medical devices. First, let’s start with device design and prototyping:
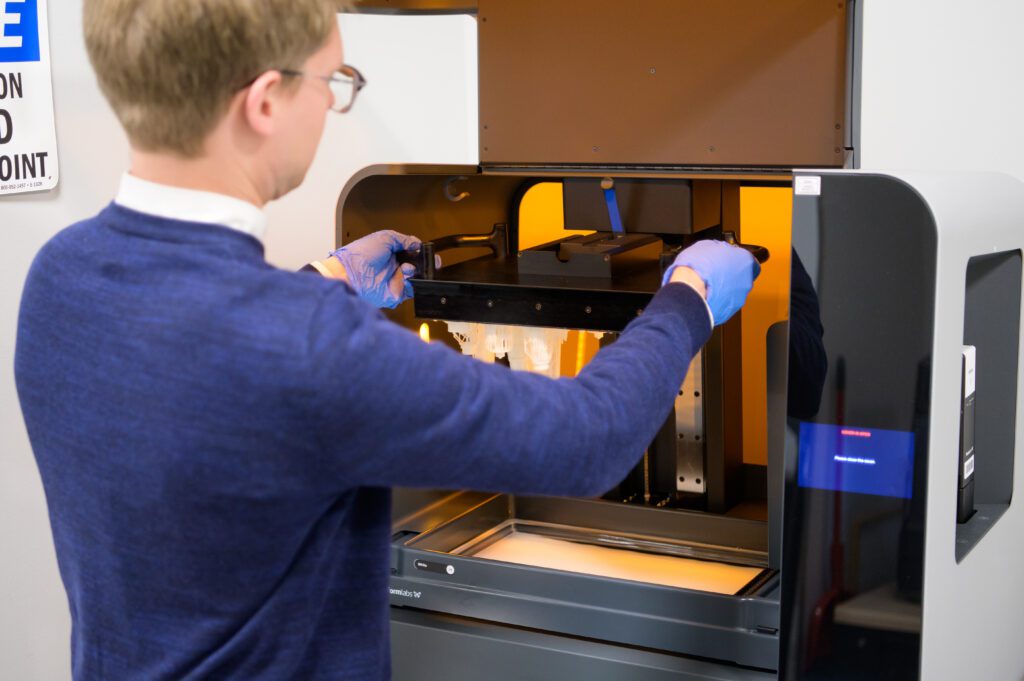
Prototyping and Product Engineering for Injection Molding
Every successful product launch begins with a thorough and well-executed prototyping process. We offer a complete range of prototyping solutions that help customers quickly turn initial concepts into validated, production-ready designs that accelerate development while minimizing risks early on.
First, we start with functional concept prototypes made of materials like PLA, ABS, or resin, using in-house SLA and FDM prototypes. These let our engineers test for failure points that can be designed out before we move on to activities with a higher cost for changing things.
Once a project enters design controls, where regulatory and engineering documentation becomes formalized, prototype activities shift from rapid iteration to production-representative builds. At this stage, parts used for testing or validation must reflect production intent in terms of both design and material.
Our design and development services include:
- 3D printing and digital simulation for concept validation
- Early-stage testing to reduce risk and accelerate time to market
- Aluminum mold tooling for rapid iterations
- In-house Design Transfer team to streamline transition to manufacturing
We move projects through these services to ensure that every design is optimized not just for performance, but also for cost-effective, repeatable production in high volumes.
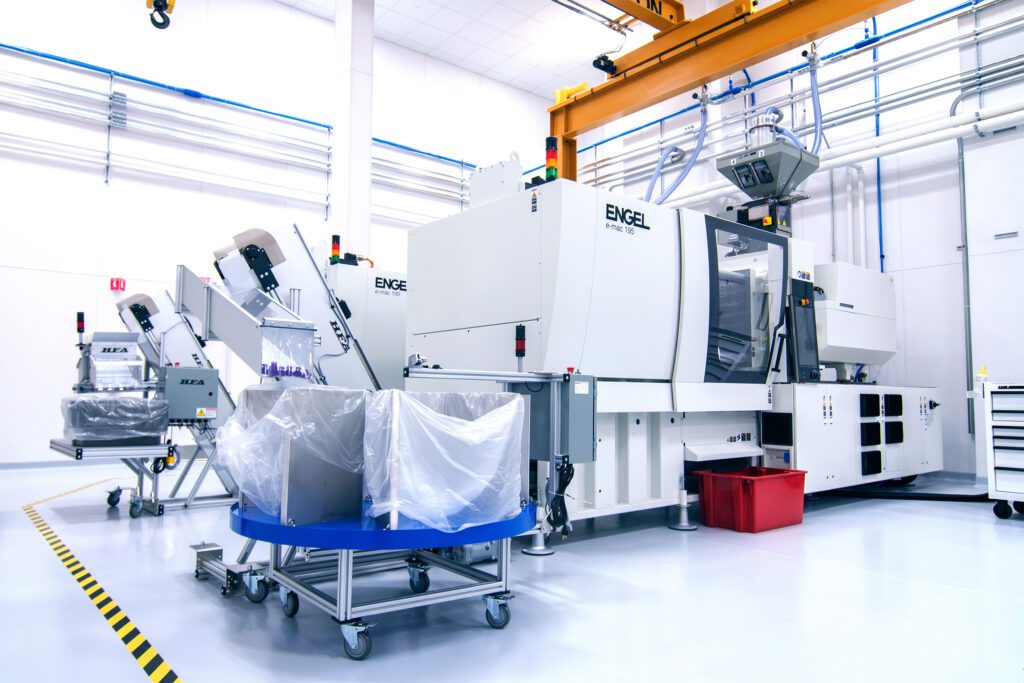
US-based Injection Molding and Manufacturing
Once the product design is ready to enter production, either for a small clinical batch or a mass production run, we verify and validate the tooling in one of our production facilities.
In the United States, our new Greensboro, NC facility is now operational and equipped to meet the growing demand for medical device injection molding and assembly.
Key highlights of this U.S. facility include:
- White room and ISO class 7 and 8 cleanroom injection molding
- Expansion opportunities for automated and manual assembly
- Close proximity to existing design and manufacturing sites in North Carolina
As part of Sanner Group, Gilero operates within an expanded global footprint, leveraging over 300,000 square feet (28,500 sqm) of total production space and more than 115,000 square feet (11,000 sqm) of ISO Class 7 and 8 cleanrooms across North America, Europe, and Asia.
Together, our combined operations bring over 60 years of expertise in molding medical and pharmaceutical components using biocompatible materials such as polycarbonate (PC), polyethylene (PE), high-density polyethylene (HDPE), polypropylene (PP), and glass-reinforced composites (GFRCs).
With these resources and molding experience, we’re able to offer a comprehensive range of injection molding services, including:
- In-house mold toolmaking & high-precision machining
- Injection molding process validation
- Mold flow analysis
- Single-cavity molds to high-cavitation hot runner systems
- Rapid prototyping and quick-turn tooling modifications
In addition to our new facility in Greensboro, our existing manufacturing sites are fully equipped to support end-to-end device manufacturing for finished medical products. These services include:
- Ultrasonic welding, heat staking, curing & annealing
- Pad and screen printing
- First article inspection & real-time process monitoring
- Form fill seal (FFS) packaging
Your One-Stop Shop for Developing Medical Devices
Bringing a medical device from concept to full-scale production is a complex process, but it doesn’t have to be complicated.
At Gilero, a Sanner Group Company, we offer everything under one roof, from early prototyping and design validation to precision mold tooling and cleanroom injection molding.
With our new Greensboro, NC facility and our global capabilities as part of the Sanner Group, we’re equipped to support projects of any size, whether it’s a small clinical run or high-volume manufacturing. Our integrated approach helps speed up development, reduce risk, and ensure the highest quality every step of the way, so our customers can focus on delivering better outcomes for patients.
Ready to bring your medical device to market faster and with confidence? Get in touch with our team today to learn we can support your next project.